一、聚光燈下,顆粒硅站上舞臺(tái)中央
1.高耗能的產(chǎn)業(yè)一環(huán)
限電年年有,今年特別嚴(yán)。
電力需求側(cè)和供給側(cè)的嚴(yán)重失衡,終究是帶來了一紙能耗雙控文件,仿佛是一夜間,全國(guó)高耗能和高排放企業(yè)站在了風(fēng)口浪尖——限電限產(chǎn)、電價(jià)上調(diào),雙重夾擊。 這浪尖上站著的,就有光伏產(chǎn)業(yè)的多晶硅料生產(chǎn)廠家。他們每生產(chǎn)1噸硅料,就需要耗費(fèi)5-6萬度電,這是什么概念?要知道,公認(rèn)的“耗能大頭”電解鋁產(chǎn)業(yè),每噸電解鋁的耗電量也不過1.35萬度。 產(chǎn)能縮減,成本上漲,導(dǎo)致硅料價(jià)格大幅提升,較去年同期已上漲了215%。其中單晶致密料已經(jīng)從2020年7月的60元/kg, 一路狂飚到現(xiàn)在的260元/kg。而供貨緊張則基本要到明年下半年才能有所緩解。
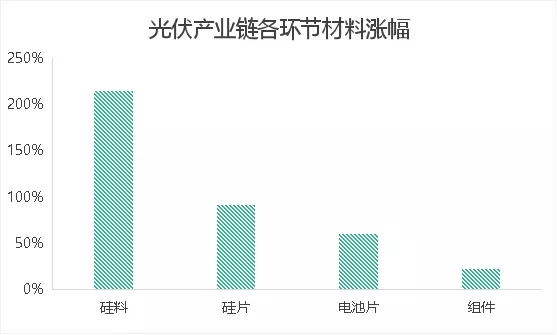
2.超節(jié)能的新星選手
11月11日,保利協(xié)鑫復(fù)牌,公布上半年凈利潤(rùn)24.07億扭虧為盈,其關(guān)鍵“王牌”顆粒硅再度引起業(yè)內(nèi)火熱關(guān)注。
在聚光燈之下,沒有什么比更節(jié)能、更低成本的硅料技術(shù)更吸引眾人的目光了!
根據(jù)保利協(xié)鑫今年8月份的調(diào)研,與改良西門子法生產(chǎn)的柱狀多晶硅料相比,用硅烷法(FBR 法)制成的顆粒硅,生產(chǎn)過程中可以使電耗降低30%、水耗降低30%、氫消耗降低42%、人員降低65%,生產(chǎn)成本總體降低30%。顆粒硅目前綜合成本3-3.5萬元/噸,棒狀硅綜合成本4-5萬元/噸,顆粒硅更具成本優(yōu)勢(shì)。
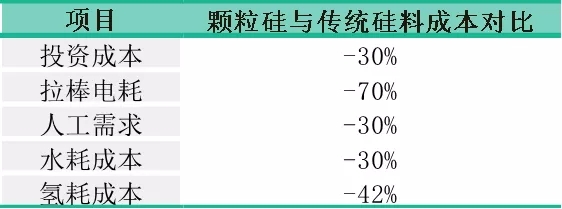
(來源:保利協(xié)鑫推介資料,浙商證券研究所整理) 不僅降本降耗,顆粒硅還“降碳排”。 保利協(xié)鑫能源半年報(bào)顯示,相較棒狀硅,每生產(chǎn)一萬噸顆粒硅將減少碳排放44.8萬噸,可節(jié)省燃煤16.64萬噸,相當(dāng)于每年多種218.6萬棵樹。 在越發(fā)緊張的能耗雙控局勢(shì)下,選擇顆粒硅,將助力高耗能硅料企業(yè)更容易通過能耗指標(biāo)、更順利地進(jìn)行擴(kuò)產(chǎn)。
3.廣闊的舞臺(tái)正在腳下
顆粒硅因其優(yōu)異的節(jié)能降本屬性,正加速對(duì)傳統(tǒng)塊狀硅的替代。
供給端方面,目前行業(yè)內(nèi),唯一掌握核心技術(shù)的協(xié)鑫顆粒硅。已實(shí)現(xiàn)萬噸級(jí)量產(chǎn)突破,并在徐州、樂山、內(nèi)蒙形成了多個(gè)十萬噸級(jí)產(chǎn)能基地,規(guī)劃顆粒硅產(chǎn)能達(dá) 50 萬噸。此外據(jù)了解,鑒于當(dāng)前巨大的需求,保利協(xié)鑫未來可能會(huì)進(jìn)一步擴(kuò)產(chǎn)。

(數(shù)據(jù)來源:保利協(xié)鑫官網(wǎng)公告、浙江證券研究所 )
需求端方面,目前隆基、中環(huán)、晶澳、雙良節(jié)能等硅片廠家紛紛“先下手為強(qiáng)”,顆粒硅采購(gòu)數(shù)量已經(jīng)接近65萬噸。
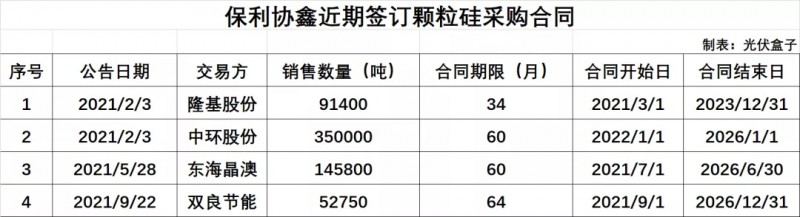
硅片企業(yè)總規(guī)模60萬噸級(jí)的采購(gòu),說明顆粒硅已經(jīng)獲得市場(chǎng)認(rèn)可,現(xiàn)在顆粒硅正處于大規(guī)模產(chǎn)業(yè)化的開端,未來顆粒硅的腳下將是一馬平川。
二、顆粒硅能否一“站”到底?
當(dāng)然,面對(duì)現(xiàn)在仍是主流技術(shù)的改良西門子法,顆粒硅技術(shù)是否能夠在硅料技術(shù)的競(jìng)技場(chǎng)上“一站到底”,更應(yīng)考慮的是,傳統(tǒng)硅料價(jià)格回落以后,顆粒硅還能不能得到下游硅片廠商的青睞。
關(guān)鍵在于能否進(jìn)一步拉開與傳統(tǒng)硅料的差距。
1.質(zhì)量差距
“硅片一哥”隆基股份曾在投資者互動(dòng)平臺(tái)上表示,“顆粒硅仍有四個(gè)缺點(diǎn):金屬含量高,碳含量高,有粉料,含氫。”
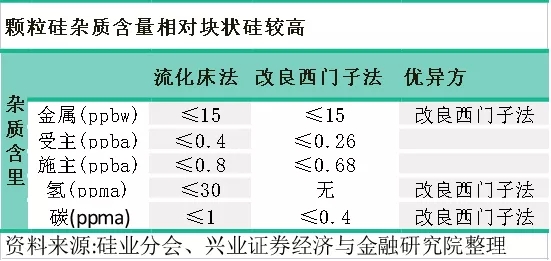
的確,顆粒硅單位體積小,暴露在外的表面積相比多晶硅更多,另外由于工藝特性顆粒硅內(nèi)部晶格更為疏松,雜質(zhì)更容易侵入。
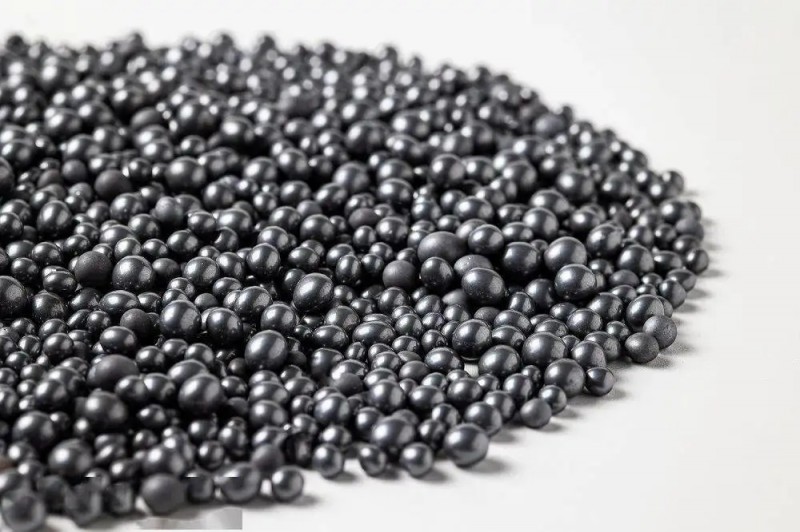
而含氫量高則是由于流化床法自身的生產(chǎn)工藝原因,較高的含氫量可能導(dǎo)致"氫跳"現(xiàn)象,即在后端拉棒環(huán)節(jié)受熱容易生產(chǎn)跳硅,從而對(duì)拉棒的穩(wěn)定性和質(zhì)量產(chǎn)生不利影響。 因?yàn)殡s質(zhì)問題,目前下游的硅片客戶主要是“摻著用”——將少量顆粒硅摻雜進(jìn)塊狀硅使用。 這就涉及到摻雜比例的問題了。在某種意義上,摻雜比例能達(dá)到多高,決定了顆粒硅未來在硅料市場(chǎng)的占比能有多大。
今年以來部分硅片廠陸續(xù)公布試用反饋,可以提供一定的參考。
上機(jī)數(shù)控在4月的調(diào)研中表示,“新投料里面用到70%甚至更高比例都是沒有問題的,還有45%的循環(huán)料,跳硅問題已經(jīng)很少了,產(chǎn)品品質(zhì)、生產(chǎn)方面都不錯(cuò)。” 中環(huán)在今年6月的調(diào)研中指出,顆粒硅的運(yùn)用比例能提高到50%以上,且對(duì)性能沒有影響。 晶澳則在今年8月的調(diào)研中表示:“大爐型的摻雜比例在40%以內(nèi),小爐型會(huì)高一些。” 綜合數(shù)據(jù)來看,上半年顆粒硅的摻雜使用表現(xiàn)都沒有什么問題。 但是仍然有進(jìn)步的空間——100%使用顆粒硅仍然大規(guī)模地生產(chǎn)n型硅片。那么顆粒硅和傳統(tǒng)硅料的差距將大大拉近。同時(shí),搭配顆粒硅更為優(yōu)秀的電性能,將更加適合下一代N型電池技術(shù),進(jìn)而進(jìn)一步搶占硅料市場(chǎng)。
2.成本差距
當(dāng)然,未來顆粒硅能否完全取代西門子法,關(guān)鍵還是取決于成本。
可以推想,當(dāng)硅料相對(duì)寬松后,兩種硅料核心比拼的就是成本。 雖然目前,根據(jù)保利協(xié)鑫的數(shù)據(jù),顆粒硅生產(chǎn)成本總體降低30%,但業(yè)內(nèi)顯然也有不同的聲音。 通威、大全和新特等硅料廠指出:“在硅料生產(chǎn)過程中,流化床法還原電耗大致6度左右,通威的西門子法40多度,兩者差異巨大。但是改良西門子法在生產(chǎn)過程中,會(huì)復(fù)產(chǎn)大量的蒸汽,解決了冷氫化的蒸汽的問題,而硅烷法是沒有的。因此,從綜合能耗看,兩種方法的不會(huì)差異特別大。”
同時(shí),他們還指出,流化床法還原爐有個(gè)內(nèi)膽,一套就是200萬,消耗很大,也會(huì)導(dǎo)致3000-4000元/噸的成本增加。 根據(jù)通威和大全的估算,顆粒硅的生產(chǎn)成本將在3.5萬元/噸左右。而通威2021年1月的調(diào)研數(shù)據(jù)顯示,其包頭一期的生產(chǎn)成本也已經(jīng)達(dá)到了3.5萬元/噸的水平。 行業(yè)測(cè)算,顆粒硅的生產(chǎn)成本目前在35元/kg左右,而2021年1月大全的調(diào)研數(shù)據(jù)顯示,其新廠和老廠最好的月份成本是38元/kg人民幣以下,新廠就36-37元/kg。 總體來看,顆粒硅當(dāng)前的生產(chǎn)成本雖然優(yōu)于西門子法的行業(yè)平均水平,但和行業(yè)先進(jìn)產(chǎn)能相比優(yōu)勢(shì)并不算大??梢灶A(yù)想,如果脫離傳統(tǒng)硅料緊缺的考慮,未來原有西門子法的廠商大概不會(huì)有太大的動(dòng)力將產(chǎn)線切換為硅烷法。
顆粒硅要想顛覆西門子法硅料,接下來仍需要瞄準(zhǔn)先進(jìn)產(chǎn)能,進(jìn)一步拉開成本差距。
三、未來拭目以待
節(jié)能低碳是顆粒硅最為突出的優(yōu)勢(shì),可以預(yù)見,這一優(yōu)勢(shì)在中國(guó)節(jié)能減排的大勢(shì)下,將會(huì)被無限放大。顆粒硅初登舞臺(tái),便引來政策長(zhǎng)遠(yuǎn)的利好。
但遙望未來,顆粒硅究竟是傳統(tǒng)硅料的補(bǔ)充,還是顛覆性的替代,還是要看質(zhì)量和成本優(yōu)勢(shì)能否再實(shí)現(xiàn)顯著提升。 差距拉得足夠開,威脅才能足夠巨大。
目前,顆粒硅的產(chǎn)能,在硅料環(huán)節(jié)的滲透率只有3%左右,未來進(jìn)步的空間非常大。而顆粒硅諸多萬噸級(jí)別項(xiàng)目已經(jīng)投產(chǎn),成本能否繼續(xù)下降,我們拭目以待。
評(píng)論